What is Porosity in Welding: Best Practices for Staying Clear Of Porous Welds
What is Porosity in Welding: Best Practices for Staying Clear Of Porous Welds
Blog Article
Porosity in Welding: Identifying Common Issues and Implementing Finest Practices for Prevention
Porosity in welding is a pervasive concern that commonly goes undetected until it creates substantial issues with the integrity of welds. This usual flaw can jeopardize the strength and durability of bonded structures, posing safety and security dangers and causing pricey rework. By recognizing the origin triggers of porosity and carrying out efficient prevention methods, welders can dramatically boost the quality and integrity of their welds. In this discussion, we will certainly discover the essential factors adding to porosity development, examine its damaging impacts on weld efficiency, and review the most effective methods that can be taken on to decrease porosity event in welding procedures.
Typical Reasons For Porosity

Another frequent culprit behind porosity is the presence of contaminants on the surface of the base metal, such as oil, oil, or corrosion. When these impurities are not properly removed before welding, they can vaporize and come to be entraped in the weld, creating defects. Furthermore, making use of unclean or damp filler materials can introduce impurities into the weld, adding to porosity concerns. To reduce these common causes of porosity, comprehensive cleaning of base steels, appropriate shielding gas option, and adherence to optimum welding specifications are vital practices in attaining high-grade, porosity-free welds.
Effect of Porosity on Weld Top Quality

The visibility of porosity in welding can considerably endanger the structural honesty and mechanical buildings of welded joints. Porosity develops voids within the weld steel, compromising its overall strength and load-bearing capability. These gaps serve as stress focus factors, making the weld much more at risk to breaking and failing under applied tons. In addition, porosity can reduce the weld's resistance to rust and various other environmental elements, better diminishing its durability and efficiency.
One of the main effects of porosity is a reduction in the weld's ductility and sturdiness. Welds with high porosity degrees tend to exhibit lower effect stamina and minimized capacity to flaw plastically prior to fracturing. This can be specifically worrying in applications where the bonded parts undergo vibrant or cyclic loading problems. Furthermore, porosity can restrain the weld's capacity to effectively transmit pressures, leading to early weld failing and possible safety and security threats in critical structures.
Ideal Practices for Porosity Avoidance
To boost the architectural stability and quality of welded joints, what certain measures can be executed to lessen the event of porosity throughout the welding procedure? Making use of the correct welding technique for the specific material being welded, such as changing the welding angle and Home Page gun setting, can additionally protect against porosity. Normal inspection of welds and immediate remediation of any issues identified during the welding procedure are important practices to avoid porosity and create premium welds.
Value of Appropriate Welding Methods
Carrying out appropriate welding methods is critical in making sure the structural integrity and quality of bonded joints, building on the structure of efficient porosity prevention measures. Welding techniques straight affect the general strength and resilience of the bonded framework. One crucial element of correct welding methods is preserving the correct warmth input. Too much warm can result in increased porosity as a result of the more entrapment of gases in the weld swimming pool. Conversely, insufficient warmth may result in insufficient blend, developing prospective weak points in the joint. In addition, utilizing the appropriate welding criteria, such as voltage, present, and take a trip speed, is essential for attaining audio welds with minimal porosity.
Additionally, the selection of welding process, whether it be MIG, TIG, or stick welding, must straighten with the particular demands of the task to guarantee ideal outcomes. Proper cleansing and prep work of the base metal, as well as choosing the appropriate filler material, are also necessary parts of skilled welding strategies. By adhering to these ideal techniques, welders can decrease the risk of porosity formation and generate top notch, structurally audio welds.
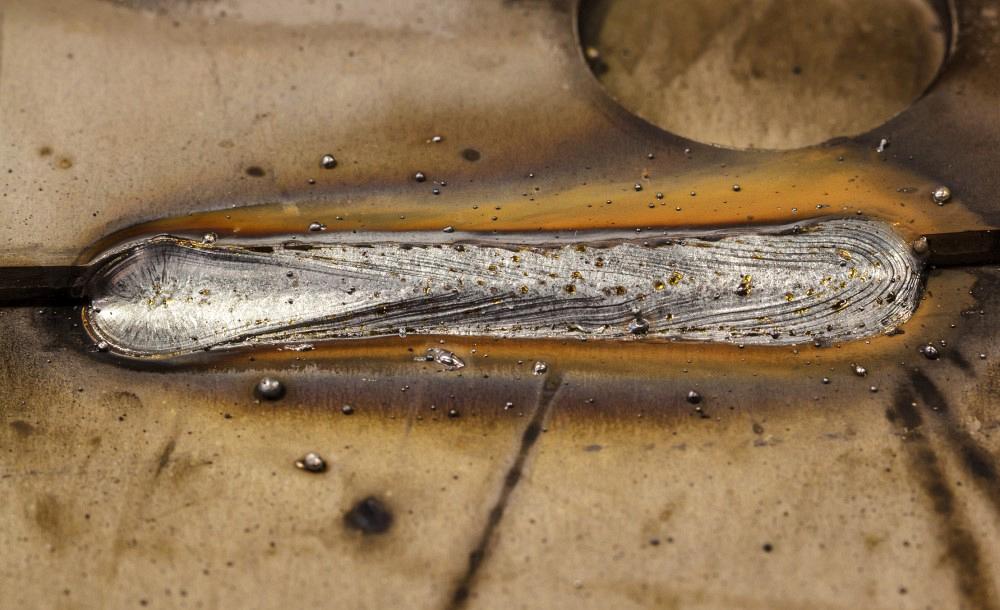
Evaluating and Quality Assurance Procedures
Quality control procedures play an essential function in validating the honesty and reliability of welded joints. Evaluating treatments are crucial to spot and avoid porosity in welding, making sure the toughness and durability of the end product. Non-destructive testing techniques such as ultrasonic screening, radiographic screening, and aesthetic assessment are generally used to recognize possible issues like porosity. These techniques allow for the assessment of weld top quality important link without compromising the stability of the joint. What is Porosity.
Conducting pre-weld and post-weld examinations is additionally vital in maintaining quality assurance requirements. Pre-weld inspections entail verifying the products, devices setups, and tidiness of the workspace to stop contamination. Post-weld examinations, on the other hand, analyze the final weld for any kind of problems, consisting of porosity, and verify that it fulfills specified criteria. Executing a comprehensive top quality control plan that consists of comprehensive screening procedures and assessments is paramount to minimizing porosity concerns and guaranteeing the total quality of welded joints.
Verdict
To conclude, porosity in welding can be a common issue that affects the high quality of welds. By determining the usual reasons of porosity and implementing best practices for prevention, such as appropriate welding methods and testing actions, welders can make certain top quality and reliable welds. It is vital to prioritize prevention techniques to reduce the occurrence of porosity and maintain the integrity of bonded frameworks.
Report this page